PAC Ilium
Ilium is a PAC (Programmable Automation Controller) with a multi-processor architecture and offers, on the same device, the main functionalities needed to implement an Industrial Automation application, with precision defined execution times:
- PLC Logic Execution;
- Motion Control;
- Communication and integration with other software components;
- Operator interface (HMI).
Through an Ethernet port that supports EtherCAT , Ilium interfaces all ISAC or third party devices, including servodrivers, inverters, sensors, I/Os.
ISAC Bridge devices add compatibility with main fieldbuses.
Ilium is available in two formats that share development tools and application libraries. The application written is portable between these two formats:
- Ilium Embedded is a powerful and compact dedicated device, and it is powerful enough to drive up to 10 EtherCAT axes. It is available with or without touch screen, it supports USB, COM ports, external HDMI video, one Ethernet port for programming and Web interfaces. It does not contain moving parts, all the components are not-removable and the CPU only needs a few Watts;
- Ilium soft-Motion is a real-time software that runs on an IPC. It exploits the flexibility and the power of the PC (provided by ISAC or by third parties) to obtain the customized operator interface. It uses in an exclusive way a part of the hardware resources: one or more cores of the CPU, a portion of RAM, one Ethernet port. Windows handles the operator interface and the functionality of web connections..
Ilium offers powerful development tools integrated in Multiprog from Phoenix Contact Software. To develop the application it is possible to use IEC61131 standard languages (Ladder Diagram; Function Block Diagram; Sequential Chard Diagram; Structured Text; Instruction List) or ANSI C.
Ilium supports and extends the set of function blocks PLCopen MC part 1 and 2, version 2.0. All discrete-movement, continuous-movement and administration FBs are available with the basic and extended interface.
Among other, you can find:
- Cams, to be programmed from the PLC logic, using the integrated Editor, or to be created from external sampling;
- Gears and electricshafts;
- Phasing;
- Slave synchronous movement, referred to the position of more Masters.
All of the movements can apply the space-based or speed-based control. The movement profile always keeps the dynamic constraints (maximum speed, acceleration, Jerk) under the desired threshold in order to obtain maximum performances without compromising the movement fluidity.
These are some of the most important integrated tools to support development:
- Axes oscilloscope: it collects synchronous dynamic information for all moving axes and thus allows the fine calibration of drivers and the verification of the movement law;
- Bus configurator: it allows to scan the available devices, to modify the map of the cyclic and asynchronous communication, to identify the status of the alarms of each device and to check their functioning, to read and write online all the parameters of the devices and to modify their maintenance, e.g., firmware update.
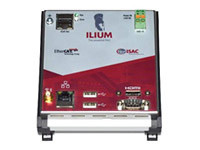